你所在的位置:首页——模具设计培训,UG编程培训交流
塑料模具设计与制作要求
作者:宁波蓝天电脑培训学校,时间:201504
塑料模具设计与制作时一个复杂的工序,我们如何来做一付完好的塑料模具呢,我们有一下几点要求
塑料模具设计与制作要求
1 范围
本标准规定了本公司塑料模具的设计与制作要求。
本标准适用于本公司的塑料模具制作与验收。
- 规范性引用标准
下列文件中的条款通过本标准的引用而成为本标准的条款。凡是注日期的引用文件,其随后所有的修改单(不包括勘误的内容)或修订版均不适用于本标准。凡是不注日期的引用文件,其最新版本适用于本部分。
Q/MB05.003-2003 塑料模具设计制造规范
3 技术要求
3.1模具的设计要求
3.1.1模具分类
根据模架尺寸将模具分为大、中、小三类。
- 模架尺寸6060以上称为大型模具;
- 模架尺寸3030~6060之间为中型模具;
- 模架尺寸3030以下为小型模具。
3.1.2模架选用与设计的要求
3.1.2.1优先选用标准模架,具体按《龙记标准模架》执行。
3.1.2.2若选用非标准模架,应优先选用标准板厚,具体参照《龙记标准模架》。
3.1.2.3大型非标模架,导柱直径不小于φ60mm,导套孔壁厚不得小于10mm,回针孔壁厚为 35~40mm,回针直径不小于φ30mm。
3.1.2.4大型非标模架A板、B板起吊螺丝孔为M36~M48。
3.1.2.5如有可能产生较大侧压力时(型腔深度超过50mm),非标大型模架应设计原身止口,以后模套住前模。
3.1.2.6模架3030以上就必须增加顶针板导柱2-4个。
3.1.2.7订购模架时必须注意方铁的高度。
3.1.3注塑参数校核方法
3.1.3.1容模尺寸校核
- 模具厚度+顶出距离+取出产品的距离<最大开模距离;
- 模具厚度>注塑机模板最小闭合距离,而<注塑机模板最大闭合距离;
- 码模板尺寸小于注塑机模板的最大装夹尺寸。
3.1.3.2锁模力:F≥P.A.S10-²
其中F:注射机的公称锁模力(t);P:模内平均压力(25~40Mpa);A:投影面积(包括产品、流道)cm²。
3.1.4型腔排位要求
3.1.4.1型腔排位有利于各腔同时、均匀进胶;
3.1.4.2多腔模各腔间距不小于20mm,大产品深腔根据强度面增加,模腔与镶件边不得少于20~25mm,多胶模的同一个产品保证进胶位置一致。
3.1.5分型面设计原则
3.1.5.1选择分型面首先必须符合要求。
3.1.5.2避免在产品外表产生夹线,如无法避免时尽量将夹线设计在不易看见的部位。
3.1.5.3为生产的产品稳定和壁厚均匀,大型模具前、后模板的分型面应增加四个或以上的
管位块;管位块必须原身留在镶件上。
3.1.5.4分型面选择应保证产品留在后模,筋位深的尽量做镶件。
3.1.5.5优先选择平面碰穿,尽量避免插穿分型面,以及薄钢位插穿。
Q/MDJ5 04.1-1—2007
3.1.5.6插穿分型面应设计2°以上的斜度,插穿面高度较小时取大斜度,插穿面高度大时取小斜度,但至少保证有0.3~0.5mm,对于不同的啤塑材料要在分型面处做出相应的排气。
3.1.5.7分型面以外超出25mm位做避空0.3mm.
3.1.6冷却系统设计要求
3.1.6.1在满足产品结构的前提下,确保冷却充分。
3.1.6.2保持运水孔大小一致:(小模)φ6~φ8、(中模)φ8~φ10、(大模)φ10~φ12。
3.1.6.3运水孔离料位距离均匀,最小不得小于:(小模)15mm、(中模)20mm(大模)25mm。
3.1.6.4各运水孔间距大约为孔径的5倍,与其它孔径间壁厚不得小于5.0mm。
3.1.6.5用隔水片方式冷却,隔水片孔为φ10时运水孔取φ6;隔水片孔径为φ12时运水孔取φ8;隔水片孔径为φ16时运水孔取φ10;隔水片孔径为φ20运水孔片取φ12;隔水片孔径间距为50~80mm时,同一组运水隔水片孔不超过6个。
3.1.6.6运水孔为φ10以下的用1/4英寸管接头,φ10以上(包括φ10)的用3/8英寸的管接头,并沉入模架内不得外露于模架外,并保持所有接头高度一致。
3.1.6.7模具进、出水孔与起吊螺丝钉孔其孔间距均不得小于40mm。而且尽量设计在注塑机背面一侧,其次为前面及底面,避免设于顶面,(防止渗水进入模腔),并标注明进出水孔方向。
3.1.6.8模具进、出水孔不得与电源处在同一平面。
3.1.7浇注系统设计要求
3.1.7.1一般水口模具的流道设计:模具定位环直径应比注塑机定位孔小0.1-0.2mm,并沉入面板5mm深。
3.1.7.2 浇口套球面半径R应比注塑机喷嘴球面半径大1.0~2.0mm;浇口套小端孔径应比注塑机喷嘴孔径大0.5~1.0mm。
3.1.7.3流道长度应尽量短,原则上不超过60mm,必要时面板要做避空减短流道。
3.1.7.4分流道应优先选用圆形,其次梯形,不得选用半圆形及矩形,流道大小根据产品材料而定,并选择相应截面的流道。
3.1.7.5流道转角用圆弧过渡,分流道末端应有冷料井。对于潜水口,冷料井位置必须低于进料口,冷料井深度约为直径的1.5倍。
3.1.7.6小水口模具的流道设计
3.1.7.6.1校核取出水口所需开模距离≯流道到产品的距离+喷嘴面到水口板面的距离。
3.1.7.6.2避免取出水口时与限位秆发生干涉,尽量将限位杆设计在模具的上、下方向。
3.1.7.7浇口位置设计要求
3.1.7.7.1能满足塑料胶材料的流动比。
3.1.7.7.2不影响产品外观以及装配,例如,夹水痕、流痕、蛇纹等。
3.1.7.7.3水口容易清除。
3.1.7.7.4 侧水口流道与产品之间的距离不得大于1.5~2.0mm,细水口尽量采用大唧嘴。
3.1.7.8. 小型电镀及丝印产品的流道应设计成环绕形流道。
3.1.8顶出机构设计要求
3.1.8.1模具顶出距离应小于注塑机的最大有效顶出行程。
3.1.8.2顶出距离确保能轻易取出产品且有限位,考虑模具方铁的有效顶出行程(订模架时注意),小模尽量可以全自动生产。
3.1.8.3顶针面避免碰穿或插穿。
3.1.8.4优先采用圆顶针,其次选用扁顶或推管,尽量避免使用推块或异形的顶针。
3.1.8.5顶针大小根据制品形状确定:一般(小模)φ5、(中模)φ8~φ10、(大模)φ12~φ16。
3.1.8.6顶针端面若为异形时应造定位防止转动,大斜面做防滑槽。电火花加工。优先采用菱形网格
3.1.8.7 柱位深度≥8mm时必须采用推管。
3.1.8.8顶针位尽量靠 近产品侧壁底部,并优先选用较大顶针。
3.1.9滑块和抽芯设计要求
3.1.9.1有效抽芯距离应大于产品倒扣尺寸3~5mm。
3.1.9.2应采用刚性抽芯方式,并设计定位装置,避免仅依靠弹簧抽芯。
3.1.9.3滑块(斜顶)应有加工限位台阶。
3.1.9.4滑块导滑部分长度大于滑块高度,导滑部位厚度不小于5mm。
Q/MDJ5 04.1-1—2005
3.1.9.5滑块不得滑出压板范围。
3.1.9.6滑动面应设计油槽。
3.1.9.7开模状态下,限位弹簧应有5~10mm预压量。
3.1.9.8斜导柱斜角一般取10°~25°,锁紧块的斜角比斜导柱斜角大2°。
3.1.9.9采用前模芯时,应保证开模状态下滑块的一半以上含在T型槽内。“T形槽全采用压条结构”,大型滑块设计在模具的模脚方向,采用油缸抽芯的滑块优/设计在模具的上方,其次再是后方、下方。
3.1.9.10斜顶抽芯设计要求。
3.1.9.10.1斜顶抽芯角度不得大于16°。
3.1.9.10.2斜顶宽度及厚度原则上不得小于10mm。
3.1.9.10.3一般小斜顶(宽度和厚度在25mm以下)采用整体形式,大斜顶采用镶件结构。
3.1.9.10.4斜顶应设计导向块,导向块厚度一般为20~40mm。
3.1.9.10.5小斜顶在顶针板上时,斜顶一般采用导滑块结构。
3.1.9.10.6斜顶抽芯距离应大于倒扣长度1.0~2.0mm以上。
3.1.9.10.7大斜顶应设计冷却系统。
3.1.9.10.8斜顶上尽量不要出胶位,防止产品包在斜顶上跟着斜顶走。
3.1.9.10.9 斜顶顶部采用三方斜面配合中,最好采用与模仁不同的材质。
3.1.10镶件设计要求
3.1.10.1深筋位或者加工、排气困难的部位应优先考虑采用镶拼结构。
3.1.10.2镶件设计应避免锐角,同时应考虑加工、装拆的方便性。必须采用螺钉、横销、台阶等方式固定,不能用烧焊或铆头方式。
3.1.10.3产品成型位置与镶件的边距一般为(小模)15~25mm、(中模)20~30mm、(大模)30~40mm,同时应考虑运水孔及螺丝钉的合理布置。
3.1.10.4 A板、B板镶件框壁厚一般为;(小模)30~50mm、(中模)50~80mm、(大模)80~120mm。
3.1.10.5开镶件框后B板厚度一般为:(小模)30~50mm、(中模)50~80mm、(大模)80~120mm。
3.1.10.6镶件成型部位厚度一般为:(小模)25~35mm、(中模)35~50mm、(大模)50~70mm。
3.1.11排气槽(针)设计要求
3.1.11.1分型面或专为排气设计的镶件应设计排气槽。
3.1.11.2排气槽相互距离为100mm~150mm,料位10mm内的深度以各种材料的溢边值为准,其余深度为0.5mm。
3.1.11.3容易困气但不能设计排气槽的部位应设计排气针。
3.1.12材料选用及热处理
3.1.12.1普通结构件(如模板、限位块、支撑柱等)一般选用45#钢。
3.1.12.2普通模具型芯、型腔一般选用P20类钢材,如: GS738、GS2311、718、NAK55等。(优先考虑客户要求)。
3.1.12.3镜面模具型芯、型腔选一般选用420类钢材,如2316、2316H、S316、S316H等。
3.1.12.4散热比较差的部位一般选用合金铜或铍铜,如Ampcoq40。
3.1.12.5要求耐磨好、韧性高的模具一般选用H13类钢淬火处理,如:H-1、8407、083等。
3.1.12.6小滑块、斜顶一般选用718氮化处理;大滑块、斜顶选用718类钢材氮化处理。
3.1.12.7导滑压板、导向块、导滑片及细小镶件一般选用T8淬火处理(不允许氮化)。
3.1.12.8所有斜顶导向块采用青铜加工。
3.1.12.9顶针、扁顶针、顶管采用SKD61,原则上不用65MN。
3.2模具的制造要求
3.2.1外观要求(钳工与设计通用)
3.2.1.1铭牌内容打印模具编号、模具重量(Kg)、模具外形尺寸(mm),字符均用1/4英寸的字码打上,字符清晰、排列整齐,铭牌厚度1mm铝片。
3.2.1.2铭牌固定在模腿上靠近后模板和基准角的地方(离两边各有15mm的距离),并加工深为0.5mm×长×宽的凹凸台,用四个铆钉固定,固定可靠,不易剥落。
3.2.1.3冷却水嘴用塑料块插水嘴φ10管,规格可为G1/8″、G1/4″、G3/8″(模具验收时应全部装配在模具上)。
3.2.1.4冷却水嘴避空孔直径为φ25×30、φ30×30、φ35×30三种规格,孔外沿有倒角,倒角大于1.5×45°,倒角一致。
3.2.1.5冷却水嘴应装上不伸出模架表面,水嘴头部凹进外表面不超过3mm。
3.2.1.6冷却水嘴有进出标记,进水为IN,出水为OUT,IN、OUT后加顺序号,如:IN01、02,OUT01、02,要求用8~12mm字码打上。
3.2.1.7进出油嘴、进出气嘴在IN、OUT前空一个字符加G(气)、O(油),字码相同。
3.2.1.8模具安装柱下方应加工有支撑腿加以保护。
3.2.1.9各模板有零件编号,编号在基准角符号正下方离底面10mm处,要求用9号,模号打在基准角的左边。
3.2.1.10模具配件影响模具的吊装和存放,如安装时下方有外漏的油缸、水嘴、先复位机构等,应加工有支撑腿保护。
3.2.1.11支撑腿的安装用螺丝穿过支撑腿固定在模架上,如果过长的支撑腿则车加工外螺纹紧固在模架上。
3.2.1.12模具顶出孔符合指定的注塑机,除小型模具外,原则上不能只用一个中心顶出(模具长度或宽度尺寸有一个大于500mm时),顶出孔直径应比顶出杆大5-10mm。
3.2.1.13定位环可靠固定(一般用三个M6或M8的内六角螺丝,大型模具用M10或以上的内六角螺丝),直径一般为φ100或φ150mm,高出顶板10mm,定位环应嵌入模板5mm,并压紧浇口套,沉入式浇口需加无头螺丝固定,防止脱落,30以下规格可不嵌入。
3.2.1.14浇口套应安装φ5防转销。
3.2.1.15浇口套球R大于注塑机喷嘴R(一般为SR20)。
3.2.1.16浇口套入口直径大于喷嘴注射口直径(大模为φ5、小模为3.5)。
3.2.1.17安装有方向要求的模具在前模板或后模板上用箭头标明安装方向,箭头旁应有“UP”和 “↑”字样,箭头和文字均用漏板喷黄色漆,字高60mm。
3.2.1.18模架表面没有凹坑、锈迹、划伤、毛刺、油污、多余不用的吊环、进出水、气、油孔等及其他影响外观的缺陷。
3.2.1.19模架各板都有大于1mm~2mm×45°的倒角。
3.2.1.20模具便于吊装、运输,吊装时不得拆卸模具零部件(油缸除外需单独包装),吊环与水嘴、油缸、先复位杆等干涉,可以更改吊环孔位置。
3.2.1.21每个重量超过10Kg 的模具零部件有合适的吊环孔,如没有,也可需要有相应措施保证零部件拆卸安装方便,吊环大小和吊环孔位置按相关企业标准设计。
3.2.1.22吊环能旋到底,吊环装平衡。
3.2.1.23顶杆、顶块等顶出机构如与滑块等干涉,要有强制先复位机构,顶板有复位行程 开关。
3.2.1.24油缸抽芯、顶出要有行程开关控制,安装可靠。
3.2.1.25油缸、进出油口要采用集中进出块。
3.2.1.26连接进出块与油缸的油管用胶管,接头用标准件。
3.2.1.27回针底下应加工有垃圾钉。
3.2.1.28支撑柱比模腿高出0.05mm—0.15mm ,并不与顶出孔干涉。
3.2.1.29锁模片安装可靠,对称安装,不少于2个,并且用红漆油表示。三板模要锁在面板与B板上。
3.2.1.30三板模前模板与水口之间有弹簧,以辅助开模。
3.2.1.31如注塑机采用延伸喷嘴,定位圈内部有足够大的空间,以保证标准的注塑机加长喷嘴带加热圈可以伸入。
3.2.1.32模具吊环孔直径必须用红色漆(如M20)。A、B板之间加工一开模槽。
3.2.2顶出、复位、抽插芯、取件的制造要求
3.2.2.1顶出时顺畅、无卡滞、无异响。
3.2.2.2模具上有斜顶或顶针直径小而数量比较多的顶针底板对应对角回针的相应位置需加工螺纹孔、以便装拆。螺纹孔以方便顶针板拆卸。模具顶针板上一定要加工顶针板回程导柱,以便斜顶、顶针的动作顺畅。
3.2.2.3斜顶表面抛光,斜顶面低于型芯0.1—0.15mm、斜顶用718材料,氮化处理并有油槽。
3.2.2.4斜顶必须加工有导向块,材料为青铜,内置在后模模架内,用螺丝固定,定位销定位。
3.2.2.5顶针端面低于型芯0—0.1mm。
3.2.2.6滑动部件必须有油槽(顶针除外),表面进行氮化处理,深度为0.06~0.2mm,硬度HRC60±2。
3.2.2.7顶针有止转定位,按图加工。顶针板能复位到底。
3.2.2.8顶出距离用限位块进行定位,限位材料为45#钢或40Cr,不能用螺丝代替,底面须平整,高度一致,位置在顶棍孔底癌
3.2.2.9复位弹簧选用标准件,两端不打磨、割断,优先选用黄色。
3.2.2.10复位弹簧安装孔底面为平底,安装孔直径比弹簧大3~4mm。
3.2.2.11直径超过φ20mm的弹簧内部有导向杆,导向杆比弹簧长10—20mm。
3.2.2.12一般情况下,选用质量比较好的矩形截面蓝色模具弹簧(轻负荷),重负荷用红色,较轻负荷用黄色。(应优先选用日本大同或者日本东发制造的弹簧)
3.2.2.13弹簧有预压缩量,预压缩量为弹簧总长的10%-15%。
3.2.2.14滑块的定位块及硬片用T8A,淬火到HRC52±2并加工油槽。
3.2.2.15滑块、抽芯有行程限位,小滑块限位用弹簧,在弹簧不便安装的情况下可用波子螺丝,油缸抽芯有行程开关。
3.2.2.16滑块抽芯一般用斜导柱角度比滑块锁紧面角度小2—3°。
3.2.2.17斜顶、滑块抽芯成型部分若有筋位、柱等难脱模的结构,应加反顶机构。
3.2.2.18大的滑块不能设在模具安装方向的上方,若不能避免,应加大弹簧或增加数量并加大抽芯距离。
3.2.2.19滑块高与长的最大比值为1,长度方向尺寸为宽度尺寸的1.5倍,高度为宽度的2/3。
3.2.2.20滑块的滑动配合长度大于滑块方向长度1.5倍,滑块完成抽芯动作后,保留在滑槽内的长度不小于滑槽长度的2/3。
3.2.2.21滑块在每个方向上(特别是左右侧)的导入角度为3~5°(配合),以利研配和防止飞边,滑块的滑动距离大于抽芯距2~3mm,斜顶类似。
3.2.2.22大型滑块(重量超过30Kg)导向T形槽,用可拆卸的压板,并加工吊环孔以方便拆卸。
3.2.2.23滑块用弹簧限位,若弹簧在里边,弹簧孔全出在模上或滑块上、若弹簧在外边,要有固定块定位。
3.2.2.24大滑块下面应加工有耐磨板硬片(滑块宽度超过150mm),耐磨板材料T8A,淬
火至HRC50±2,耐磨板比大面高出0.05-0.1mm,耐磨板应加油槽。
3.2.2.25大型滑块(宽度超过200mm)锁紧面应加工有耐磨板硬片高出1mm上面加油槽。
3.2.2.26宽度超过250mm滑块,在下面中间部位是否增加一至数个导向块,材料为T8A,淬火至 HRC52±2.
3.2.2.287若产品有粘前模的趋势,后模侧壁加皮纹或保留火花纹,无加工较深的倒扣,无手工打磨加倒扣筋或麻点。
3.2.2.28若顶针上加工倒钩方向需保持一致,并且倒钩易于从产品上去除。
3.2.2.29顶针沉头的尺寸,包括直径和厚度不允许私自改动,或垫垫片,顶针沉头与顶针底板虚位不超过0.05mm。
3.2.2.30顶针孔与顶针的配合长度应为顶针直径2-3倍、顶针孔用铰刀加工,其余部位的孔径比顶针直径大1mm~2mm。顶针上表面磨出,异形的用铣刀铣出或电火花蚀出,顶针不允许上下串动。
3.2.2.31产品顶出对易跟着斜顶走,顶针上加槽或蚀纹,并不影响制品外观。
3.2.2.32有推板顶出的情况,顶针为延迟顶出,防止顶白。
3.2.2.33回针端面平整,无点焊,胚头底部无垫垫片、点焊。
3.2.2.34固定在顶针上的顶块可靠固定,四周非成型部分应加工3~5°的斜度,下部周边倒角。
3.2.2.35三板模水口板导向滑动顺利,水口板易拉开。
3.2.2.36所有导套底部要加排气口,以便将导柱进入导套时形成的封闭空腔的空气排出,尺寸做成 10×1用铣刀铣出,不允许用倒角机。
3.2.3冷却水路的制造要求
3.2.3.1冷却水道充分、畅通,符合图纸要求(间隙不大于60mm),钻运水后,再吹干净孔里的铁屑,
采用铜塞要有台阶孔并铰孔/或用无头螺丝堵住。
3.2.3.2密封可靠、无漏水、易于检修,水嘴安装时缠生料带,并注意缠生料带方向。
3.2.3.3放置密封圈的密封槽按相关企业标准加工尺寸和形状,并开设在模架上(按图加工),深度为防水圈厚度×0.75。
3.2.3.4水道隔水片采用不易受腐蚀的材料,一般用黄铜片或铝片(较深时原则上不用采用此方式)。
3.2.3.5前、后模采用集中运水方式。
3.2.4一般浇注系统(不含热流道)的制造要求
3.2.4.1浇口套内主流道表面要抛光至▽1.6(标准件)。
3.2.4.2浇道要抛光至▽3.2或400#沙纸。
3.2.4.3三板模分浇道出在A板背面的部分截面应为梯形。
3.2.4.4三板模在水口板上断料把,浇道入口直径小于φ2,球头处有凹进口板的一个深3mm的台阶。
3.2.4.5小水口模具浇口套应加工成3~5°锥度并与水口板相配用无头螺丝固定,也可以用压板压住。
3.2.4.6水口板和前模板之间的开距应适于取料把,一般情况下,大于130mm。
3.2.4.7三板模前模板限位用限位杆,且四支限位杆,长度相差不大于0.1mm,限位杆孔上模部分加工深度相差不大于0.1mm。(等高螺丝)
3.2.4.8浇口、流道按图纸尺寸用机床(电脑锣、铣床、电火花)加工,不允许手工打磨或打磨机加工。
3.2.4.9点浇口浇口处按浇口规范加工。
3.2.4.10点浇口处前模有一小凸起,后模相应有一凹坑。
3.2.4.11分流道前端有一段延长部分作为冷料穴。
3.2.4.12拉料杆Z形倒扣圆滑过渡。全自动生产的小模采用攻丝的方式。
3.2.4.13前后模流道错位不超过0.1mm,流道转角处需采用R0.5~R2圆弧过渡。
Q/MDJ5 04.1-1—2005
3.2.4.14出在顶针上的潜伏式浇口不允许表面收缩。
3.2.4.15透明产品冷料穴的直径、深度符合设计标准(按图纸加工)。
3.2.4.16水口料应易于去除,产品外观面无浇口痕迹,产品有装配处无残余水口料。
3.2.5热流道系统的制造要求
3.2.5.1热流道接线布局合理、易于检修,接线有线号并一一对应。
3.2.5.2进行安全测试,以免发生漏电等安全事故。
3.2.5.3每一组加热元件应有热电偶控制,热电偶布置位置合理,以精确控制温度。
3.2.5.4喷咀出料口部尺寸小于φ5mm,以免因料把大而引起制品表面收缩。
3.2.5.5分流板与模板之间有隔热垫隔热,可用石棉网、不锈钢等。
3.2.5.6温控表设计定温度与实际显示温度误差小于±2°C,并且控温灵敏。
3.2.5.7热流道接线捆扎,并用压板盖住,以免装配时压断电线。
3.2.5.8控制线有护套,无损坏,一般为电缆线,电线不露在模具外面。
3.2.5.9分流板或模板所有与接触的地方圆角过渡,以免损坏电线。
3.2.5.10在模板装配之前,所有线路无短路现象。
3.2.5.11所有电线正确连接、绝缘。
3.2.6成型部分、分型面、排气槽
3.2.6.1前后模表面没有不平整、凹坑、锈迹、划伤、打磨等其他影响外观的缺陷。
3.2.6.2镶块与模框配合,四R角是否低于1mm的间隙(最大处)。
3.2.6.3分型面保持干净、整洁,无手提砂轮打磨避空,封胶部分无凹陷。
排气槽深度小于塑料的溢边值,PP小于0.03mm,ABS、PS等小于0.05mm,排气槽由机床加工,无手工打磨痕迹。
3.2.6.4镶件、镶芯等可靠定位固定,圆形件有止转,镶块下面不垫铜片、铁片,如烧焊垫起,烧焊处形成大面积接触并磨平。
3.2.6.5前模光洁度按产品要求抛光到位。
3.2.6.6前模及后模筋位、柱位表面,无火花纹、刀痕,并尽量抛光,丝筒、针孔表面用铰刀精铰,无火花纹、刀痕,顶针端面与型芯一致。
3.2.6.7插穿部分大于2°的斜度(或至少大于0.3mm插穿位),以免起刺,插穿部分无薄刃结构。
3.2.6.8模具后模正面用油石去除所有纹路、刀痕,火花纹,如未破坏可保留(但一定要全部一样规格),平面要求磨出。
3.2.6.9模具各零部件有编号。
3.2.6.10前后模成型部位无倒扣倒角等缺陷。
3.2.6.11深筋(超过15mm)用镶拼。筋位顶出顺利。
3.2.6.12一模数腔的制品,如是左右对称,注明L或R,深 柱(超过8mm)用丝筒,字号为1/8″。
3.2.6.13多腔模具须用反字码在型芯的适当位置打上顺序号,加以区别。(指出打印方式同上)。
3.2.6.14顶针布置在离侧壁较近处以及筋、凸台的旁边,并使用较大顶针。
3.2.6.15分型面封胶部分符合设计标准(中型以下模具10-20mm,大型模具30-50mm其余部分机加工避空)。
3.2.6.16皮纹及喷砂需达到要求。
3.2.6.17产品表面要蚀纹或喷砂处理,拔模斜度为3~5°,或皮纹越深斜度越大。(可参照益新 板)
3.2.6.18有外观要求的产品螺钉柱用防缩措施。
Q/MDJ5 04.1-1—2005
3.2.6.19深度超过20mm的螺丝柱用司筒针。
3.2.6.20螺丝柱如有倒角,相应司筒、镶针相应倒角。
3.2.6.21产品壁厚均匀(0.15mm以内)。
3.2.6.22斜顶、滑块上的镶芯有可靠的固定方式,(螺丝紧定或有胚头从背面插入)。
3.2.6.23模具材料包括型号和处理状态按合同要求。
3.2.6.24透明件前后模是否抛光至镜面。
3.2.6.25除型腔、型芯成型部位以外,所有的棱边和孔均有1mm~2mm×45°的倒角,倒角机倒后修顺。上模原装凹进,周边无料位、边全用R角(由电脑锣铣出),下模凸出部分相应R角加大R2~3(由电脑锣铣出)。
3.2.6.26如有焊接的部位须修顺,不得有明显的氧化层,不允许存在烧焊痕迹。
3.2.6.27所有零部件均不得有锈斑、油污、毛刺,并有字码标识,字码要沉入镶件。
3.2.6.28模具零部件加工中一般不得使用打磨机,如余量过多时应重新上机床加工。
3.2.6.29模架型腔、型芯各表面不得有对刀痕迹。
3.2.7包装的制造要求
3.2.7.1模具型腔喷防锈油,滑动部件涂黄油,浇口套进料口用黄油堵死。
3.2.7.2模具安装锁模片,并且规格符合设计要求(三板模脱料板与后模固定)至少两片。
3.2.7.3模具产品图纸、结构图纸、水路图纸、零配件及模具材料供应商明细、使用说明书、装箱单、电子文档间应齐全。
3.2.7.4模具外观是否喷蓝漆。
3.2.7.5备品、备件易损件应齐全并附明细。
3.2.7.6模具用薄膜包装,用木箱包装是否油漆喷上模具名称、放置方向,木箱应固定牢靠。
你所在的位置:首页——模具设计培训,UG编程培训交流
学校活动
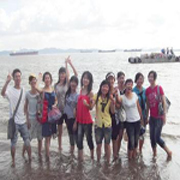
象山一日游
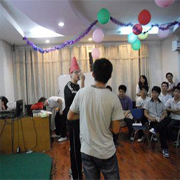
中秋晚会
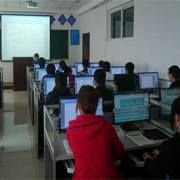
上课现场
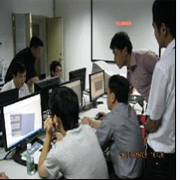
辅导讨论
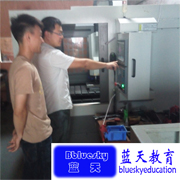
实习现场