培训课程
- 办公软件
- CAD制图
- proe培训
- ug培训
- solidworks培训
- CATIA培训
- Rhino犀牛培训
- Autodesk inventor培训
- 平面设计培训
- 网页设计培训
- 数控编程培训
- 模具设计
- 淘宝开店培训
- 电脑维修
- 室内设计
- 建筑CAD
- 3dmax培训
- protel99电路
认证考试
学历教育
你所在的位置:首页-模具设计培训技术交流
模具设计培训模具电极的介绍
作者:宁波蓝天教育咨询有限公司 时间:14/11/23
模具加工中的电极是什么东西
一种是:电火花加工的放电端,用来加工型腔、刻字等,多制作成所需形状,材料为石墨、铜或铝(少见)。另一种是:线切割加工的放电端,材料为钼丝,它的原理是通过电控部分对其施加高频高电压,当电极(钼丝)与接地端(工件)接触时,即形成高频打火产生高温,将与钼丝接触的工件面(极小的一条缝)迅速溶掉,即所谓的线切割
。
所谓多电极加工,是指要加工的部位要求的精度比较高,对放电部位要进行2次或者两次以上放电,前期为平动较大的粗放电加工,后期为平动小的精放电加工
电极就是电火花放电加工的放电点,金属的,预先做好形状,通过加工给工件上电腐蚀出规定的形状。
一个火花机要加工一个工件需要不止一个电极,不同的活要用不同的电极
因为粗加工时用一个电极打效率,但是损耗比较大,粗打后换另外一个电极精打,但是电极的装卡需要很高的精度,再有就是电极找正什么的,总之是个很需要经验的活,因为再次装卡导致的误差很可能会影响模具的精度误差。不过现在用快速夹具应该可以解决吧,伊罗哇夹具很好不过就是太贵几万块吧。
我不是搞模具的,我是搞火花机的,知道的没专门搞模具的多,一些问题只是根据我自己的理解回答的
UG的我也没听过,至于画电极我觉得画电极加工路径似乎人没有计算机准确吧,你这里说的画电极是不是根据模具的样子来制作电极吧,说画是先把要做的电极图纸画出来啊,这个对模具加工是第一步啊,很重要的
模具加工中的打电极是什么?技术点在哪里?
就是在两电极(工件和铜公)通上电流,在其间充满电介质(如煤油),当两电极相当接近时,其间的电介质被击穿,形成间隙放电,通过放电产生的高温高压使金属腐蚀从而得到所需的形状。电火花加工可以加工传统切削加工无法加工的型面,可以加工高硬度材料等。其缺点是加工过程缓慢,且不能加工非导电材料。对加工影响较大的主要有脉冲电流和脉冲频率等参数。
电火花加工与线切割又有什么区别呢?
电火花加工和电火花线切割加工都是通过间隙放电腐蚀工价加工。不同的是线切割是使用钼丝切割出所需的轮廓形状。简单的说,电火花加工能加工盲孔,而线切割加工只能加工通孔
数控电火花线切割快走丝慢走丝区别?
快走丝在专业术语中叫做:高速往复走丝电火花线切割机
慢走丝在专业术语中叫做:低速单向走丝电火花线切割机
二者的特点:
往复走丝电火花线切割机床的走丝速度为6~12 m/s,产品的最大特点是具有1.5度锥度切割功能,加工厚度可超过1000mm以上,,应用于各类中低档模具制造和特殊零件加工,成为我国数控机床中应用最广泛的机种之一。但由于往复走丝线切割机床不能对电极丝实施恒张力控制,故电极丝抖动大,在加工过程中易断丝。由于电级丝是往复使用,所以会造成电极丝损耗,加工精度和表面质量降低。
低速走丝线切割机电极丝以铜线作为工具电极,一般以低于0.2m/s的速度作单向运动,在铜线与铜、钢或超硬合金等被加工物材料之间施加60~300V的脉冲电压,并保持5~50um间隙,间隙中充满脱离子水(接近蒸馏水)等绝缘介质,使电极与被加工物之间发生火花放电,并彼此被消耗、腐蚀,在工件表面上电蚀出无数的小坑,通过NC控制的监测和管控,伺服机构执行,使这种放电现象均匀一致,从而达到加工物被加工,使之成为合乎要求之尺寸大小及形状精度的产品。目前精度可达0.001mm级,表面质量也接近磨削水平。电极丝放电后不再使用,而且采用无电阻防电解电源,一般均带有自动穿丝和恒张力装置。工作平稳、均匀、抖动小、加工精度高、表面质量好,但不宜加工大厚度工件。由于机床结构精密,技术含量高,机床价格高,因此使用成本也高。
可成形深孔及复杂形状的塑件。
塑料在热与压力下,通过模具浇注系统,加热迅速而均匀,保证硬化时间较短。
塑件尺寸精度容易保证,分型面飞边薄。
对流动性小于 80mm 的塑料挤胶较为困难。
成形压力比压胶法大。
耗用塑料须增加(浇注部分)。
3) 注射法:将粒状或粉状塑料在注射机料筒内受热熔化到流动状态,然后用很高压力和较差快的速度,通过一个狭小的喷嘴和模具的浇注系统,充满整个型腔,经过一定时间的定形,开启模具,即可从模具中取出塑件。 注射成形的特点:
成形周期短,容易实现。
塑件尺寸精度容易保证。
模具通常设计成固定式,塑件金属嵌件较多时,嵌件的安装就较困难。
4.3.2 塑料模具按成形方式分类
可分为:热固性塑料压胶模、热固性塑料挤胶模、热固性塑料注射模及热塑性塑料注射模。
热固性塑料压胶模按加工料腔的形式又可分为:
(a)敞开式压胶模,即型腔就是加料腔;
(b)半封闭式压胶模,即加料腔的截面;
(c)封闭式压胶模即加料腔本身就是型腔的延续部分,成形压力通过上模完全传到被压制的塑料件上。
按结构形式可分为:
(a)移动式压胶模,
(b)固定式压胶模。
5. 影响电加工质量的因素
影响加工质量的原因是多方面的,大致与电极材料的选择、电极制造、电极装夹找正、加工规准的选择、操作工艺是否恰当等有关。要防止产生废品,应注意下列各点。
5.1 正确选择电极材料
在型腔加工中,石墨是常用的电极材料,但由于石墨的品种很多,不是所有的石墨材料都可作为电加工的电极材料,应该使用电加工专用的高强度、高密度、高纯度的特种石墨。紫铜电极常用于精密的中、小型型腔加工。在使用铸造或锻造制造的紫铜坯料做电极时,材质的疏松、夹层或砂眼,会使电极表面本身有缺陷、粗糙和损耗不均匀,使加工表面不理想。
5.2 制造电极时正确控制电极的缩放尺寸
制造电极是电火花加工的第一步,根据图纸要求,缩放电极尺寸是顺利完成加工的关键。缩放的尺寸要根据所决定的放电间隙再加上一定的比例常数而定。一般宁肯取理论间隙的正差,即电极的标称尺寸要偏“小”一些,也就是“宁小勿大”。若放电间隙留小了,电极做“大”了,使实际的加工尺寸超差,则造成不可修废品。如电极略微偏“小”,在尺寸上留有调整的余地,经过平动调节或稍加配研,可最终保证图纸的尺寸要求。 在型孔加工中无论是制造阶梯电极,还是用直接加工电极,由于最终要控制凸凹模具的配合间隙,因此对电极缩放尺寸的要求是十分严格的,一般应控制在±0.01mm。
5.3 把好电极装夹和工件找正的第一关
在校正完水平与垂直,最后紧固时,往往会使电极发生错位、移动,加工时造成废品。因此,紧固后还要不厌其烦地再找正检查一下,甚至在加工开始进行了少量进给后,还需要停机再查看一下是否正确无误。因为电火花加工开始阶段是很重要的一个环节,也是需要操作者最精心的时候。
由于电极装夹不紧,在加工中松动,或找正误差过大,是造成废品的一个原因。电极或辅助夹具的微小松动,会给加工深度带来误差。有时在多次重复加工中,加工条件相同,但深度误差分散性很大,往往也是电极松动造成的。加工过程中夹具发热,也会使电极松动。对于一些小型单电极,只用一个螺栓与电极连接固定,则更容易发生松动,特别是石墨电极采用这种夹固方法 是非常不可靠的。
在进行型孔加工中,一般为了减少加工量,都进行预铣或预钻。加工留量越小,越有利于提高加工速度,但也会给找正带来困难,造成废品的潜在危险也越大,多型孔同时加工的场合更是如此,由于预铣、预钻孔的尺寸不够均匀一致,往往多数孔已经找正,而有一二个孔略偏。如果观察粗略,就有可能加工后个别型孔留有“黑皮”而造成废品。因此在加工初始阶段,一定要停机查核,确实无误后再继续加工。
5.4 要正确选用加工规准,了解脉冲电源的工艺规律
了解和掌握脉宽、脉间、电流、电压、极性等一组电规准对应产生的电极损耗、加工速度、放电间隙、表面粗糙度以及锥度等工艺效果,是避免产生废品、达到加工要求的关键。不控制电极损耗就不能加工出好的型腔,控制不好粗糙度和放电间隙,就不能确定最佳平动量,修光型腔侧壁。控制不准放电间隙和粗糙度就加工不出好的型孔。常常有人埋怨电源的电极损耗异乎寻常的大,这往往是由于极性接反了,或者是用高频、窄脉宽进行型腔的粗加工。
5.5 防止由于脉冲电源中电气元件的影响而造成废品
脉冲电源在维修中由于更换了元器件,使脉冲参数发生改变,也会使加工达不到人们预期的效果。或由于电源中元器件损坏、击穿,引起拉弧放电,也是造成工件严重破坏的原因。
5.6 注意实际进给深度由于电极损耗引起的误差
在进行尺寸加工时,由于电极长度相对损耗会使加工深度产生误差。而由于规准变化的不同,误差也会很不一致,往往使实际加工深度小于图纸要求。因此一定要在加工程序中,计算、补偿上电极损耗量,或者在半精加工阶段停机进行尺寸复核,并及时补偿由于电极损耗造成的误差,然后再转换成最后的精加工。 5.7 正确控制平动量
型腔或型孔的侧壁修光要靠平动,既要达到一定粗糙度的要求,又要达到尺寸要求,需要认真确定逐级转换规准时的平动量。否则有可能还没达到修光要求,而尺寸已经到限,或者已经修光但还没有达到尺寸要求。因此,应在完成总平动量 75%的半精加工段复核尺寸,之后再继续进行精加工。
5.7 防止型腔在精加工时产生波纹和黑斑
在型腔加工的底部及弯角处,易出现细线或鱼鳞状凸起,称为波纹。产生的原因有以下几方面:
电极损耗的影响:电极材料质量差,方向性不对,电参数选择不当,造成粗加工后表面不规则点状剥落(石墨电极)和网状剥落(紫铜电极)。在平动侧面修光后反映在型腔表面上就是“波纹”。
冲油和排屑的影响:冲油孔开得不合理,“波纹”就严重;另外排屑不良,蚀除物堆积在底部转角处,也助长了“波纹”的产生。 减少和消除的方法:
采用较好的石墨电极,粗加工开始时用小电流密度,以改善电极表面质量。
采用中精加工低损耗的脉冲电源及电参数。
合理开设冲油孔,采用适当抬刀措施。
采用单电极一修正电极工艺,即粗加工后修正电极,再用平动精加工修正,或采用多电极工艺。
精加工留在型腔表面的黑斑常常给最后的加工带来麻烦。仔细观察这部分的表面不平度较周围其他部分要差。这种黑斑常常是由于在精加工时脉冲能量小,使积留在间隙中的蚀除物不能及时排出所致。因此,在最后精加工时要注意控制主轴进行灵敏的“抬刀”,不使炭黑滞留而产生黑斑。
5.8 注意装夹在一起的大小电极在放电间隙上的差异(此处主要指侧面间隙)
原则上放电间隙应不受电极大小的影响,但在实际加工中,大电极的加工间隙小,而小电极加工间隙反而偏大,一般认为:
大小电极组装精度可能不一样,小电极垂直精度不易装得象大电极那样高,使其投影面积增大,造成穿孔加工放电间隙扩大。
小电极在穿孔加工过程中容易产生侧向振动,造成放电间隙扩大。
由于穿孔进给速度受大电极的限制,使小电极二次放电机会增多,致使其放电间隙扩大。
5.9 防止硬质合金产生裂纹
由于硬质合金是粉末冶金材料,它的导热率低。过大的脉冲能量和长时间持续的电流作用,都会使加工表面产生严重的网状裂纹。因此,为了提高粗加工的速度而采用宽脉宽、大电流加工是不可取的。一般宜采用窄脉宽(50μs 以下)高峰值电流,短促的瞬时高温使加工表面热影响层较浅,避免裂纹发生。
5.10 防止在型孔加工中产生“放炮”
在加工过程中产生的气体,集聚在电极下端或油杯内部,当气体受到电火花引燃时,就会象“放炮”一样冲破阻力而排出,这时很容易使电极与凹模错位,影响加工质量,甚至报废。这种情况在抽油加工时更易发生。因此,在使用油杯进行型孔加工时,要特别注意排气,适当抬刀或者在油杯顶部周围开出气槽、排气孔,以利排出积聚的气体。
5.11 注意热变形引起的电极与工件位移
在使用薄型的紫铜电极时,加工中要注意由于电极受热变形而使加工的型腔产生异常。
另外值得注意的是停机后,由于人为的因素,使电极与工件发生位移。在开机时,又没注意电极与工件的相对位置,常常会使接近加工好的工件报废。
5.12 注意主轴刚性和工作液对放电间隙的影响
电火花加工的蚀除物从间隙排出的过程中,常常在电极与工件间引起电极与加工面的二次放电。二次放电的结果使已加工过的表面再次电蚀,在凹模的上口电极进口处,二次放电机会就更多一些,这样就形成了锥度。电火花加工的锥度一般在 4′~ 6′之间。二次放电越多,锥度越大。为了减小锥度,首先要保持主轴头的稳定性,避免电极不必要的反复提升。调节好冲、抽油压力,选择好适当的电参数,使主轴伺服处于最佳状态,既不过于灵敏,也不迟钝,都可减少锥度。在加工深孔中为了减少二次放电造成锥度超差,常采用抽油加工或短电极的办法。
5.13 要密切注视和防止电弧烧伤
加工过程中局部电蚀物密度过高,排屑不良,放电通道、放电点不能正常转移,将使工具工件局部放电点温度升高,产生积炭结焦,引起恶性循环,使放电点更加固定集中,转化为稳定电弧,使工具工件表面积炭烧伤。
防止办法是增大脉间及加大冲油,增加抬刀频率和幅度,改善排屑条件。发现加工状态不稳定时就采取措施,防止转变成稳定电弧。
电极制造工艺
石墨在加工前应在油里浸透好,以便在机械加工时,石墨屑不易飞扬,清角线和棱角线不易剥落。 石墨和紫铜电极采用一般的机械加工(车、铣、刨、磨等),最后钳工修正成形。
紫铜电极还可采用线切割加工。 一般对于形状比较简单的型腔,多数采用单电极成形工艺,即采用一个电极,借助平动扩大间隙,达到修光型腔的目的。所谓单电极,可以是独块电极,也可以是镶拼电极,这由电极加工工艺而定。 对于大中型及型腔复杂的模具,可以采用多电极加工,各个电极可以是独块的,也可以是镶拼的,视具体情况而定。
.使用低损耗电源还可以把型腔的整体加工改为型腔的局部加工。
考虑到经济效益,在能够采用机械加工的地方尽量用机械加工,对复杂型腔,四周清角、底部圆弧及窄槽等无法用机械加工的地方,则采用局部加工。此外也可采用整体加工和局部加工相结合的方法,即先用石墨电板加工出大致的形状,然后再用紫铜电极进行局部加工。上述方法均取得很好的效果。
选择不同的电极材料,把整体加工分解为局部加工
过去型腔电加工绝大多数采用石墨电极,极少采用紫铜电极。那是因为过去型腔模电火花加工绝大多数采用整体加工方式,而且那时虽然也有晶体管和可控硅脉冲电源,但是电极损耗较大,尤其在精规准时,损耗可达 25~30%,不适宜作局部加工。而且大块石墨容易找到,容易制作,并且份量轻,可磨削,易加工,因而被大量采用。而铜电极,由于大块紫铜难找,磨削困难,再加上电极损耗后,钳工修正困难,因此大大限制了紫铜电极的使用。 随着低损耗电源问世以来,型腔电加工工艺也随之由整体加工逐渐转为局部加工,不再需要大块电极,因此,紫铜电极应运而生。局部加工的电极不需要很大,但是几何形状较复杂,尺寸精度要求高,因此,人们采用紫铜作为局部加工的电极。
线切割和电火花加工配套应用 中精加工低损耗电源输出功率较小,生产率略低,加工模具的双面间隙在 0.1~0.25mm 左右。目前人们还是采用平动方法,扩大间隙来达到修光型腔的目的,但是平动方法也有它的不足之处,仿形精度受到一定影响,四周会产生圆角,底部产生平台,因此平动量不宜太大,一般为 0.1~0.3mm。因而确定了电极的缩放量为 0.1~0.3mm。根据型腔模具设计原则,电极尺寸的缩放按几何方法计算,因此在电极设计时只要在技术要求上写明电极的缩放量即可。 目前国内的线切割机床都有间隙补偿装置。线切割机床可利用间隙补偿装置自行切割电极。
如果采取线切割与电火花加工配合应用,可简化电极设计,保证电极质量,提高工效,缩短制造周期。 在电火花加工型腔模具工艺中,除了利用低损耗电源扩大电加工应用范围及线切割与电加工配合应用外,还有许多方法可以提高型腔模的精度,采用 X、Y、Z、U、C 五轴数控联动(X 水平方向,Y 水平方向,Z 垂直方向,主轴转动 U,主轴分度运动 C),采用自动交换电极的电火花加工中心,只要事先调整好电极和编好相应的程序,便能自动加工复杂模具。
更多请点击-模具设计培训技术交流
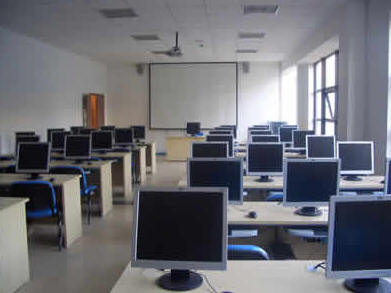
联系方式
电话:15906845558 尹老师 QQ:41780253理论教学地址
宁波江东百丈东路1130号海运港420室